11 Things Needed to Start a Chemical Etching Plant
11 Things You Need to Start a Chemical Etching Plant
Chemical etching has been around since 2500 BC and was primarily used for making jewelry. Etching is now used for making many different parts. It is used for making PCBs, flexible circuits, flexible heaters, metal screens, metal filters, glass products, semiconductors, solar panels, and much more.
If you are making parts from sheet metal, you need to seriously look at chemical etching. Sheet metal is perfect for the etching process and depending on your quantity can be the most economical process available.
This article was written so you can learn what is required to start a chemical etching plant and learn a little about each process required for etching metal. Chemical etching is also known as photo etching, photochemical etching, metal etching, and acid etching.
The 11 Things you need to start a chemical etching plant are:
- Inspection/Material Preparation
- Chemical cleaner
- Resist Application. Dry film laminator or liquid resist
- Exposure Unit
- Developer
- Etcher
- Stripper
- Inspection for Quality Control
- Waste Treatment
- A Facility
- Environmental Clearances
Keep reading to learn about each step and the approximate up-front investment needed for each process.
1. Inspection/Material Preparation (Non-Chemcut Product)
Inspection tools can vary depending on what exactly you are looking to etch. For inspection before etching, you are looking at tools to measure your material to make sure you have the correct size (Tape measure, calipers, and scales).
You may want a tool to check the material hardness if you have certain specs you need to stay within. There are so many inspection tools out there it really depends on what your shop needs. There is no one size fits all.
For preparation, you may need a cutting tool to cut the material to the correct size. If you are cutting a sheet of metal, you may want a deburr for the edges so you don’t cut your hands.
Once again, preparation tools are not a one size fits all. It will depend on what you are trying to etch.
Approximate Cost = $75,000
2. Chemical Cleaner (Chemcut Product)

Chemical cleaning is a necessary process to ensure resist adheres to the metal properly. Without proper adhesion the resist will lift, and you will lose resolution.
In the world today that cannot happen. Everything is getting smaller and smaller so any resolution lost could completely ruin the part.
Most chemical cleaning processes have two steps. Starting with an alkaline clean which removes all oil/organics from the surface.
Then rinsed and cleaned again with acid which cleans the rest of the contaminants off the surface. The acid clean also micro etches the surface which adds roughness to the surface.
The rougher surface allows for better resist adhesion.
Depending on your product and how tight your specs are there are other cleaners available. They include scrubber, deburr, electrolytic cleaner, and ultrasonic cleaner.
Approximate Cost = $150,000
3. Resist Application (Non-Chemcut Product)

Applying resist is a relatively easy process. The key point to focus on with resist is to talk with your supplier and make sure you select the resist best suited for your application.
Certain resist is designed to work best with copper, steel, glass, and so on. So, make sure to match your resist with your metal/ceramic.
Once you determine your material and the resist type that matches it. You need to look at the resolution each resist offers.
Typically, thinner resists offer better resolution because it allows the etchant to get in and out of the channel easier.
Liquid resists are thinner and offer greater resolution, but the application process is more difficult than dry film.
Approximate Cost = $40,000
4. Exposure Unit (Non-Chemcut Product)
As everything keeps getting smaller this has become one of the most important steps. A speck of dirt is enough to cause an open circuit on fine lines. The slightest misalignment on artwork top to bottom has the potential to shift dimensions outside the tolerances.
There are many different exposure units on the market now. Most do a very good job, but there are a few things that are important to have to make sure you can etch fine features.
Those features are collimated light (or LDI) and features that help create near perfect alignment. You will also need a yellow room. Keeping the yellow room and material clean will help you significantly.
The last tip we have is to hold the panel for 30 minutes after exposing it so the resist can lock into the metal more before developing it.
Approximate Cost = $200,000
5. Developer (Chemcut Product)
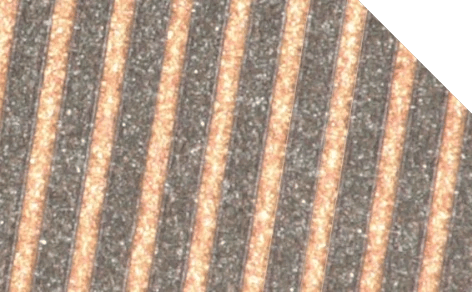
The developer is used to dissolve the photoresist that was not exposed to the UV light in the above step. Removing the unpolymerized resist exposes the metal you would like to etch away. This provides you with the design you want to etch into your material.
Developing is normally looked at as less critical than etching. This is true, BUT it doesn’t mean you can overlook the developing step. The photoresist can be underdeveloped or overdeveloped.
Underdeveloped means all the unpolymerized resist was not completely removed. So, you did not fully expose the metal that you want to etch away. This results in smaller holes or no breakthrough for chemical milling and shorts for circuits.
Overdeveloping will cause the developer solution to start undercutting the resist. This can cause your resist to lift while etching and reduce your etch quality. With resist lifting, you may not meet the specifications you need or you may receive open circuits.
Approximate Cost = $92,000
6. Etcher (Chemcut Product)

The etcher is where the metal removal happens and is the most critical piece of wet processing equipment. Like photoresists, the chemistry used in the etcher needs to be matched with the metal you want to etch.
What is so critical about the etcher?
The etch uniformity is first and foremost. To have great etch uniformity you need to have the solution moving. If the solution sits on one spot for too long the solution becomes less or non-reactive.
This causes poor etch uniformity. This is known as the puddle effect.
Secondly, transport is important. Most material thickness has no issue in the developer because all the metal is there, and the photoresist adds to the thickness. However, during etching, the metal is being removed.
That means the panel is becoming less rigid and prone to wrapping around a roller. (Most transportation issues only apply to thin material processing)
Buying an etcher that has great etch uniformity and transportation is key to building a successful etching shop.
Approximate Cost = $97,000
7. Stripper (Chemcut Product)

Stripping the photoresist from the metal is the next step. As a whole stripping is less technical than the other wet processes. Basically, the resist needs to be in the chemistry long enough to strip.
There are a couple of important factors to consider if you want an efficient stripping line.
First, you will need to check with your chemical and photoresist supplier to ensure that they are compatible with each other. If they are not compatible you will see your resist stripping off in sheets, as goo, as large pieces, or very fine pieces. All of which can create problems for your equipment and process.
You want your resist to strip in small chips. The reason you want small chips is that strippers are designed to filter out small chips. If you are getting any other size or goo, this means your resist and chemistry are a mismatch, and the stripper will have a hard time filtering out particles.
This will result in plugged nozzles.
Secondly, you will want to decide what design is best for your shop. Are you running high volume or just a couple of boards a day? This will help you determine how the filtering is set up.
You will also want to understand how the filtering works. If the machine you select does not filter the resist well, you will experience lots of downtime due to nozzle clogging.
No one wants down time, so make sure your stripper has an adequate filtering system.
Approximate Cost = $103,000
5 – 7. DES (Develop – Etch – Strip)
Many etching shops put all three of these processes in one line. This allows shops to use less operators because the panel will go through all three processes before it needs to be unloaded.
There are some negatives to putting all three together. The line is much larger, so you need a large room.
The processes do not run at the same speed so some chambers may need to be larger than a stand-alone machine. If you move forward with opening a shop a Chemcut employee can help you through this decision process.
Approximate Cost = $360,000
8. Inspection for Quality Control (Non-Chemcut Product)
The tools needed for inspection after etching will be microscopes, calipers, pin gauges, micrometers, or automated inspection tool. Just like before etching there are many options here and it will depend on your budget.
If you are etching screens, fine lines and spaces, or just a lot of small features the automated inspection tool is great!
However, automated inspection equipment is expensive. So, microscopes, pin gauges, calipers, and micrometers tend to be the go to quality inspection tools used in etching shops.
Approximate Cost = $75,000
9. Wastewater Treatment (Chemcut Product)
There are multiple options for wastewater treatment, but the most popular is a batch wastewater treatment. A batch wastewater treatment system will consist of a collection tank, a treatment tank, filter press, clear well tank, ion exchange, and final tank.
The collection tank will collect all the runoff from your wet processing equipment. All your machines will have some liquid leaving the system. Mostly from your rinses.
The wastewater that is collected can be transferred to the treatment tank (precipitation tank). The wastewater will be treated here, and all the metals will precipitate to the bottom of the tank.
The clear water can be decanted into the clear well tank and if all the metals are removed the water can be transferred to the final tank. From the final tank, the water can be pH corrected and sent down the drain.
The metals (sludge) that settles at the bottom of the treatment tank will be pumped through the filter press. The filter press will remove all the sludge and this sludge can then be shipped off your facility as toxic waste.
The last piece of equipment you will need is a scrubber for the fumes that are being pulled out of your wet processing line.
Approximate Cost = $350,000
10. Facility (Non-Chemcut Product)
If you do not have a facility yet, we recommend talking to an equipment manufacturer so you can plan your facility around the needed equipment. If you already have a facility, no problem.
Most machines can be designed to fit into the space available. However, like mentioned above, purchasing a DES line may be more difficult if your facility is not large enough.
If your facility is too small for a DES line the machines can be broken up into three separate machines or into two. You can have a develop – etch or etch – strip line made to save on operator cost.
Approximate Cost = 15 – 20% of total equipment investment
11. Environmental Clearances (Non-Chemcut Product)
The cost of environmental clearances will depend on your local and state regulations.
What you will want to do is find out how much chemistry you can have on site.
What are the limits on heavy metals for discharging?
Are any of the chemicals you want to use heavily regulated?
What size scrubber does your local government require you to have?
Getting answers to these questions will help you determine what all you need and if you can feasibly start a chemical etching plant in your current location.
Approximate Cost = ??? This depends on where you are located. Check with your local authorities.
Starting a chemical etching plant is not as easy as “just get an etcher and start making parts.” Building a chemical etching plant requires thorough planning, a large up-front investment, and time to study the process so you experience as little downtime as possible.
We did not put this article together to discourage you from building your plant, we put this together, so you know what it requires to start a successful chemical etching plant. We are here to help you succeed!
Approximate Overall Cost = $1,395,000