Conveyorized Chemical Glass Etching and Cleaning Equipment
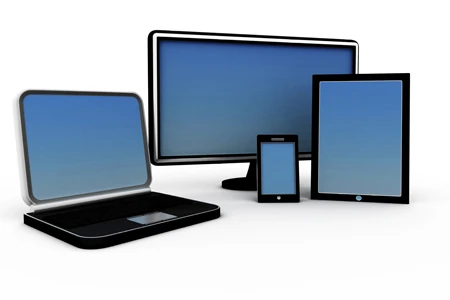
How Do You Etch Glass?
Glass etching—silicon etching, Si etching—can be completed chemically, mechanically, or with a laser. Chemcut specializes in building chemical glass etching machines.
Chemical etching can result in a clear, see-through surface or a frosted, matte finish.
Etching glass for a see-through surface is completed using HF plus another acid. If you need to remove some material but keep the optical properties, then chemical etching is a great solution for glass thinning.
Creating decorative glass through chemical engraving is a fast and cost-effective solution. You can utilize a glass frosting solution to engrave the pattern into the surface for a matte finish or an HF etching solution to engrave grooves.
There are many chemical formulas for glass etching. The most common glass etching solutions we see are:
- HF and Nitric acid (Glass Etcher)
- HF and sulfuric acid (Glass Etcher)
- HF and Ammonium Fluoride (Glass Frosting)
- Ammonium Bifluoride (Glass Frosting)
Advantages of Chemical Glass Etching
Etching to Strengthen: Etching increases the strength of glass by removing the external layer, which is weakened by defects.
Micro-cracks are common issues with mechanical and laser etching, but not with chemical etching. Chemical etching removes or “rounds out” micro-cracks, significantly lowering crack propagation.
No chipping along the etched surface and non-etched surface.
Unlimited complexity: All features are etched at the same time, so there is no added machining cost to produce more complex parts.
Fast Machining Process: Glass etching may be slow relative to metal etching, but it is fast relative to laser and mechanical machining. Laser and mechanical machining can only make one part at a time, so it is much slower than chemical etching.
No expensive hard tooling: Since the tooling process is digital, prototyping and design changes are fast and easy.
Our wet processing equipment is ideal for a variety of glass manufacturing projects—flat panel displays (FPD), cell phones, large frosted windows, small frosted parts, solar panel silicon cleaning or etching, and others.
The flexibility of our XLi, CC8000, and 2300 Series allows equipment for glass products to be built with a broad range of process steps, dwell times, and rinsing configurations.
Compared to heavy steel components, Chemcut’s lightweight conveyor construction reduces the possibility of damage to thin glass substrates. Standard conveyor configurations can accommodate piece sizes from 5–60 inches wide and 6–80+ inches long
Chemcut Wet Processing Equipment for a Range of Glass Projects
Chemcut has manufactured equipment for a variety of specialized glass processes:
Glass Cleaning Machine
- Chemical Glass Cleaner
- Mechanical Glass Cleaner
Glass Etcher
- HF Etcher
- Glass Thinning
- Glass Frosting Machine
Glass Photoresist developer
View Commonly Used Wet Processing Machines for Glass and Flat Panel Display Manufacturing
XLi with External Automatic Pressure Adjust
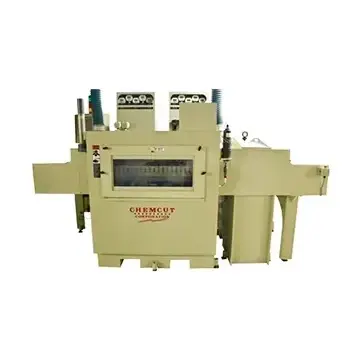
Control the spray pressure of each spray tube using the PLC instead of the throttling screw.
- 20″
- 30″
- 40″
- 50″
- 60″
- Custom Size (1 to as many chambers as you want)
- DES (Develop – Etch – Strip)
- Etcher (Stand Alone)
- SES (Strip – Etch – Strip)
- Alkaline Etchant
- Cupric Chloride Etchant
- Ferric chloride Etchant
- Hydrofluoric Acid (HF)
- Micro etch
- Aluminum
- Copper
- Glass
- Steel
- Titanium
- And more
XLi Developing Systems
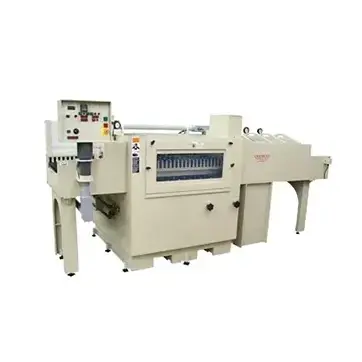
- 20″
- 30″
- 40″
- 50″
- 60″
- Custom Size (1 to as many chambers as you want)
- Developer (Stand Alone)
- DES (Develop – Etch – Strip)
- 1% Potassium Carbonate
- 1% Sodium Carbonate
XLi Etching Systems
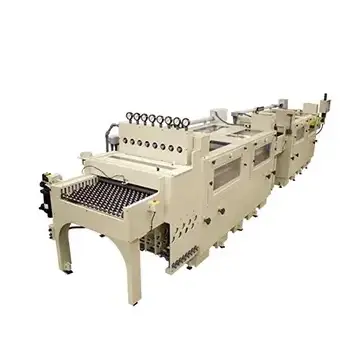
- 20″
- 30″
- 40″
- 50″
- 60″
- Custom Size (1 to as many chambers as you want)
- DES (Develop – Etch – Strip)
- Etcher (Stand Alone)
- SES (Strip – Etch – Strip)
- Alkaline Etchant
- Cupric Chloride Etchant
- Ferric chloride Etchant
- Hydrofluoric Acid (HF)
- Micro etch
- Aluminum
- Copper
- Glass
- Steel
- Titanium
- And more
XLi Chemical Cleaning System
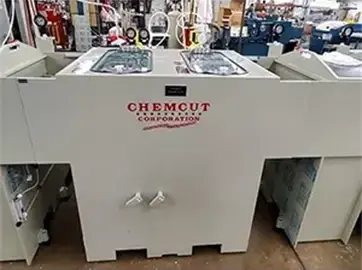
- 20″
- 30″
- 40″
- 50″
- 60″
- Cleaner (Stand Alone)
- Alkaline Clean to Acid Clean
- Custom Size (1 to as many chambers as you want)
- Acid Cleaner
- Alkaline Cleaner
XLi Stripping Systems
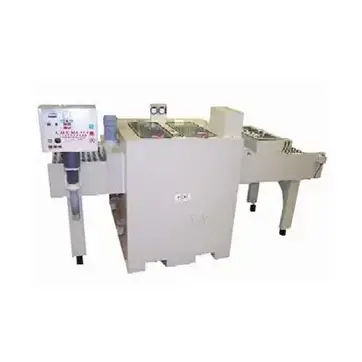
- 20″
- 30″
- 40″
- 50″
- 60″
- Custom Size (1 to as many chambers as you want)
- DES (Develop – Etch – Strip)
- SES (Strip – Etch – Strip)
- Stripper (Stand Alone)
- Metal Resist Stripper
- Proprietary Aqueous or Semi-Aqueous Stripper
- Potassium Hydroxide
- Sodium Hydroxide
2300 Series Chemical Cleaning System
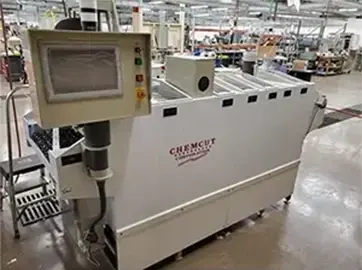
- 15″
- 20″
- 30″
- Cleaner (Stand Alone)
- Alkaline Clean to Acid Clean
- Custom Size (1 to as many chambers as you want)
- Acid Cleaner
- Alkaline Cleaner
2300 Series Developing System
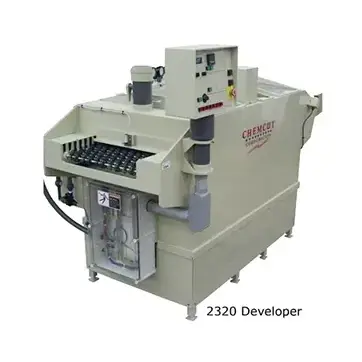
- 15″
- 20″
- 30″
- Custom Size (1 to as many chambers as you want)
- Developer (Stand Alone)
- DES (Develop – Etch – Strip)
- 1% Potassium Carbonate
- 1% Sodium Carbonate
- dry film photoresists
- liquid photoresists
- Aqueous solder mask resist (dry and liquid)
- And many more resists
2300 Series Dryer
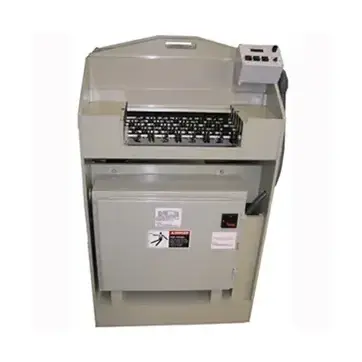
- 15″
- 20″
- 30″
- 40″
- Stand-alone drying system
- Portable unit (move anywhere in the shop) or fix it in place
2300 Series Etching System
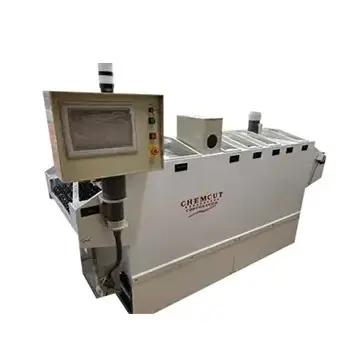
- 15″
- 20″
- 30″
- Custom Size (1 to as many chambers as you want)
- DES (Develop – Etch – Strip)
- Etcher (Stand Alone)
- SES (Strip – Etch – Strip)
- Alkaline Etchant
- Cupric Chloride Etchant
- Ferric chloride Etchant
- Hydrofluoric Acid (HF)
- Micro etch
- Aluminum
- Copper
- Glass
- Steel
- Titanium
- And more
2300 Series Stripping System
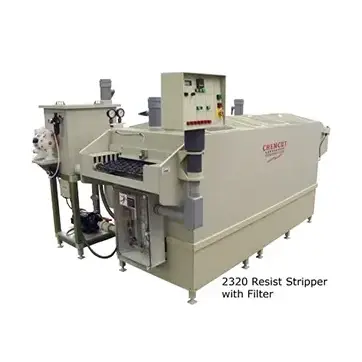
- 15″
- 20″
- 30″
- Custom Size (1 to as many chambers as you want)
- DES (Develop – Etch – Strip)
- SES (Strip – Etch – Strip)
- Stripper (Stand Alone)
- Metal Resist Stripper
- Proprietary Aqueous or Semi-Aqueous Stripper
- Potassium Hydroxide
- Sodium Hydroxide
CC8000 Chemical Cleaning System
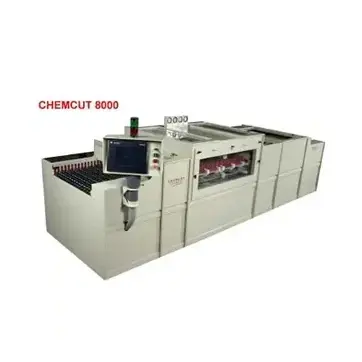
- 20″
- 30″
- 40″
- 50″
- 60″
- Cleaner (Stand Alone)
- Alkaline Clean to Acid Clean
- Custom Size (1 to as many chambers as you want)
- Acid Cleaner
- Alkaline Cleaner
CC8000 Developing Systems
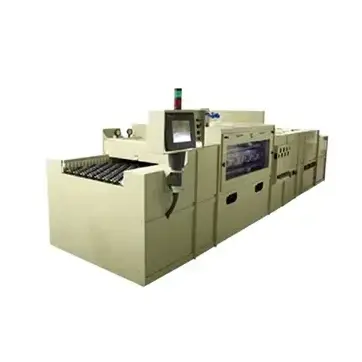
- 20″
- 30″
- 40″
- 50″
- 60″
- Custom Size (1 to as many chambers as you want)
- Developer (Stand Alone)
- DES (Develop – Etch – Strip)
- 1% Potassium Carbonate
- 1% Sodium Carbonate
- dry film photoresists
- liquid photoresists
- Aqueous solder mask resist (dry and liquid)
- And many more resists
CC8000 Etching Systems
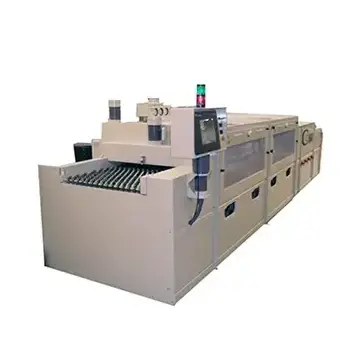
- 20″
- 30″
- 40″
- 50″
- 60″
- Custom Size (1 to as many chambers as you want)
- DES (Develop – Etch – Strip)
- Etcher (Stand Alone)
- SES (Strip – Etch – Strip)
- Alkaline Etchant
- Cupric Chloride Etchant
- Ferric chloride Etchant
- Hydrofluoric Acid (HF)
- Micro etch
- Aluminum
- Copper
- Glass
- Steel
- Titanium
- And more
CC8000 Stripping Systems
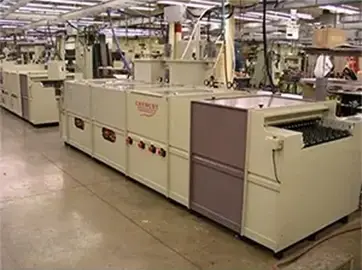
- 20″
- 30″
- 40″
- 50″
- 60″
- Custom Size (1 to as many chambers as you want)
- DES (Develop – Etch – Strip)
- SES (Strip – Etch – Strip)
- Stripper (Stand Alone)
- Sodium Hydroxide
- Potassium Hydroxide
- Proprietary Aqueous or Semi-Aqueous Stripper
- Metal Resist Stripper
121 Brush Cleaner
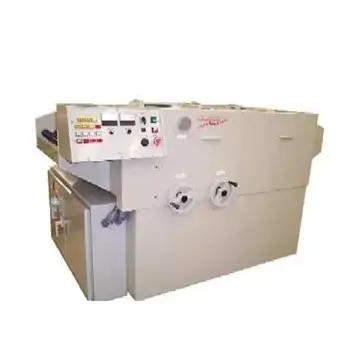
- Wet Brushing
- Oscillating Brushes
- Choice of bristle or compressed brushes
- Brushing
- Cleaner
- Finishing
- Remove Polishing
219 Scrubber
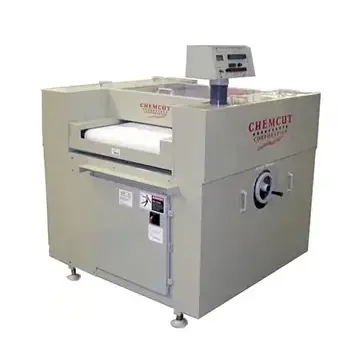
- Single-sided abrasive brush
- Tough reinforced conveyor belt supports small parts
990D Electroless Plating System
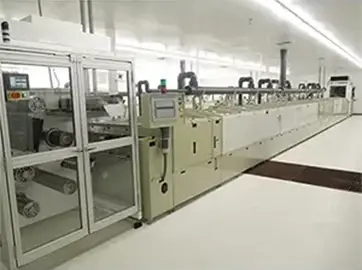
Product Lines for Electrolytic and Electroless Plating: CC8000, Dip Tanks, XLi, 2300 Series
- Desmear
- Electroless Copper Plating
- Electroless Nickel Plating
- Electrolytic Copper Plating
- Electrolytic Gold Plating
- Electrolytic Silver Plating
- Electrolytic Tin Plating
- Immersion Gold Plating
- Immersion Silver Plating
- Immersion Tin Plating
- Ni/Au Plating
- PTH (Plated through-hole) Any discussion on this topic should include your chemistry supplier as well. It is critical that the bath for PTH is monitored closely.
- Inner layer bonding operations: brown oxide (Bondfilm, Multibond, etc.), (white ‘oxide’ – immersion Tin)
Related Resources
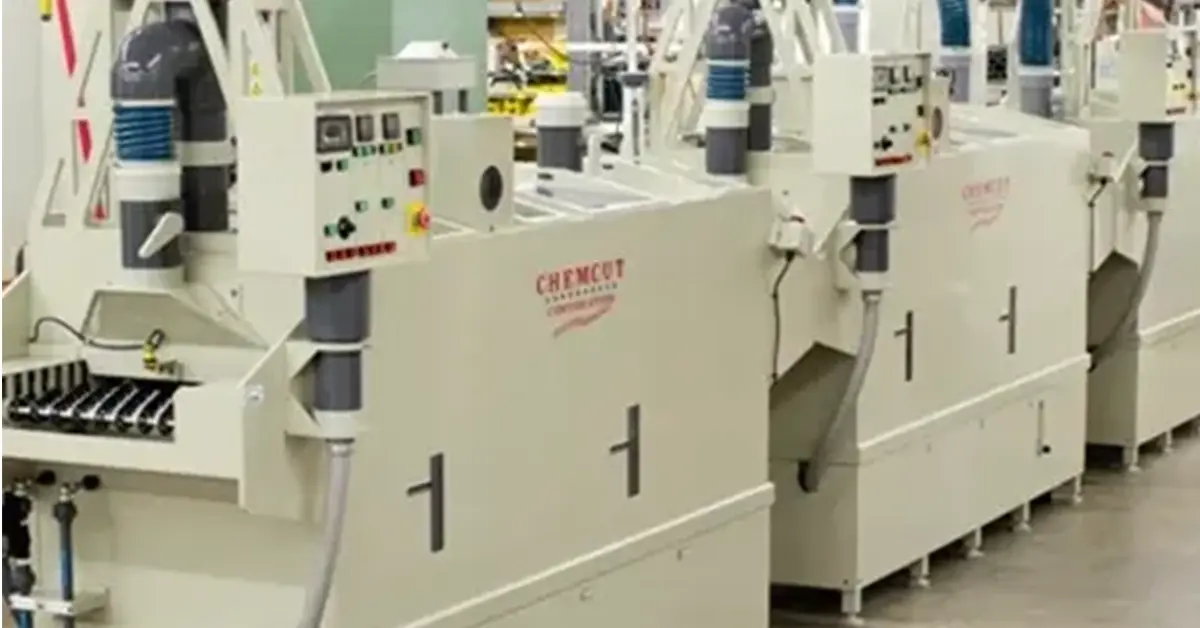
11 Things Needed to Start a Chemical Etching Plant | Chemcut Blog
11 Things You Need to Start a Chemical Etching Plant Chemical etching has been around since 2500...
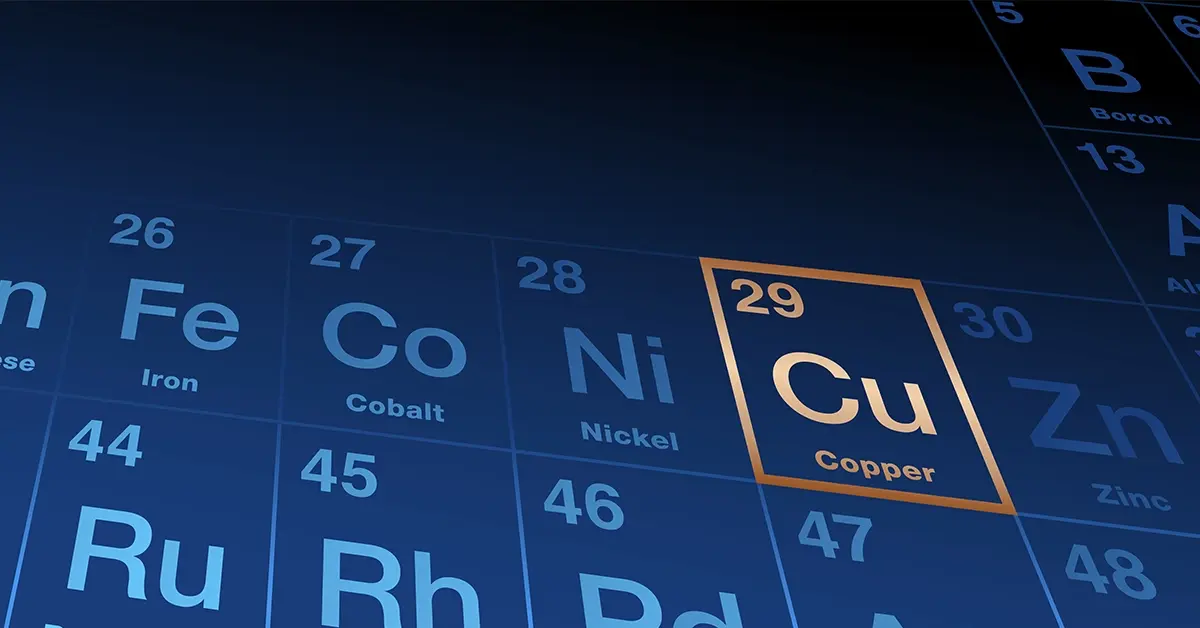
Copper Etchant Options | ChemCut
Copper etching is a vital manufacturing process that tends to be used in the manufacturing of...

Understanding The etching Process
Chemical etching is a widely used technique in the manufacturing industry for selectively removing...
High quality products are made with high quality equipment. Stake your reputation on Chemcut.
Already a customer?
Chemcut’s commitment to you goes beyond the sale. We keep your equipment running with the industry’s best post-sales support, which includes our in-house R&D lab and global field service assistance.
We also maintain the industry’s largest and most diverse inventory of high-quality replacement parts to ensure prompt delivery regardless of the type or age of your Chemcut or MEI Division equipment.