Photoresist Stripping Machines
Product Lines for Photoresist Stripping
Explore our diverse range of photoresist stripping product lines, each readily tailored to suit your specific process. When you are ready, contact our expert team to design the solution you need.
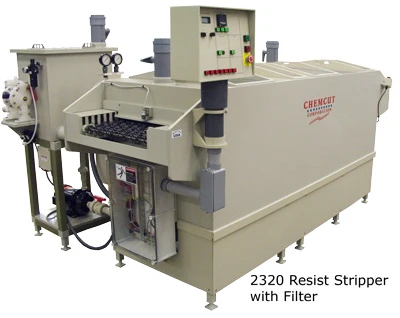
XLi Stripping Systems
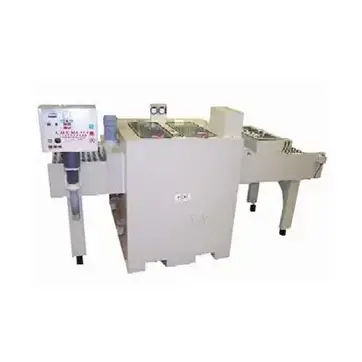
- 20″
- 30″
- 40″
- 50″
- 60″
- Custom Size (1 to as many chambers as you want)
- DES (Develop – Etch – Strip)
- SES (Strip – Etch – Strip)
- Stripper (Stand Alone)
- Metal Resist Stripper
- Proprietary Aqueous or Semi-Aqueous Stripper
- Potassium Hydroxide
- Sodium Hydroxide
2300 Series Stripping System
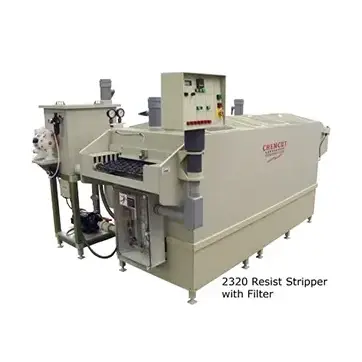
- 15″
- 20″
- 30″
- Custom Size (1 to as many chambers as you want)
- DES (Develop – Etch – Strip)
- SES (Strip – Etch – Strip)
- Stripper (Stand Alone)
- Metal Resist Stripper
- Proprietary Aqueous or Semi-Aqueous Stripper
- Potassium Hydroxide
- Sodium Hydroxide
CC8000 Stripping Systems
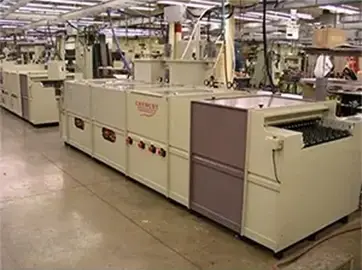
- 20″
- 30″
- 40″
- 50″
- 60″
- Custom Size (1 to as many chambers as you want)
- DES (Develop – Etch – Strip)
- SES (Strip – Etch – Strip)
- Stripper (Stand Alone)
- Sodium Hydroxide
- Potassium Hydroxide
- Proprietary Aqueous or Semi-Aqueous Stripper
- Metal Resist Stripper
Photoresist Stripping Process
The photoresist stripping process follows the wet etching step and is less technical than the other wet processes. Basically, the resist needs to be in the chemistry long enough to strip. We build strippers for positive photoresist and negative photoresist.
There are a couple of important factors to consider if you want an efficient stripping line. First, work with your chemistry and photoresist film supplier(s) to make sure your resist and chemistry are compatible. If they are not compatible, the resist will strip off in sheets, as goo, as large pieces, or as very fine particles.
None of the results are good!
You want your resist to strip in small chips, because our strippers are designed to filter out small chips.
If you are getting any other size, or goo, then your resist and chemistry are a mismatch. Your Chemcut stripper will have a hard time filtering out particles, resulting in plugged nozzles.
Chemcut’s stripping machines are designed with world-class filtering, which will increase your line’s efficiency, speed, and cleanliness.
Stripping resist creates a lot of small particles, which can cripple your throughput if not filtered correctly. We design our strippers to have a clean sump and a dirty sump, enabling us to separate as many particles as possible from the spray and return stripper solution to the clean sump after filtration.
The dirty sump contents are pumped through our on-board resist filter, then on our bulk separator.
This design has helped many chemical etching plants optimize their throughput by decreasing downtime and maintenance time on their stripper module.
Chemcut also offers a range of high-pressure options for the sometimes-difficult task of removing photoresist after a plating step. Pump and spray pressures of 100 psi up to 500 psi are possible. A high-pressure station can be added to our XLi or CC8000 modular systems easily, if needed. Check out our other options that can be added to your stripping machine.
We encourage you to take advantage of our ability to test your chemistry for compatibility in our testing laboratory. We can also do spraying tests, Which will result in more accurate photoresist stripping time estimates.
Related Resources
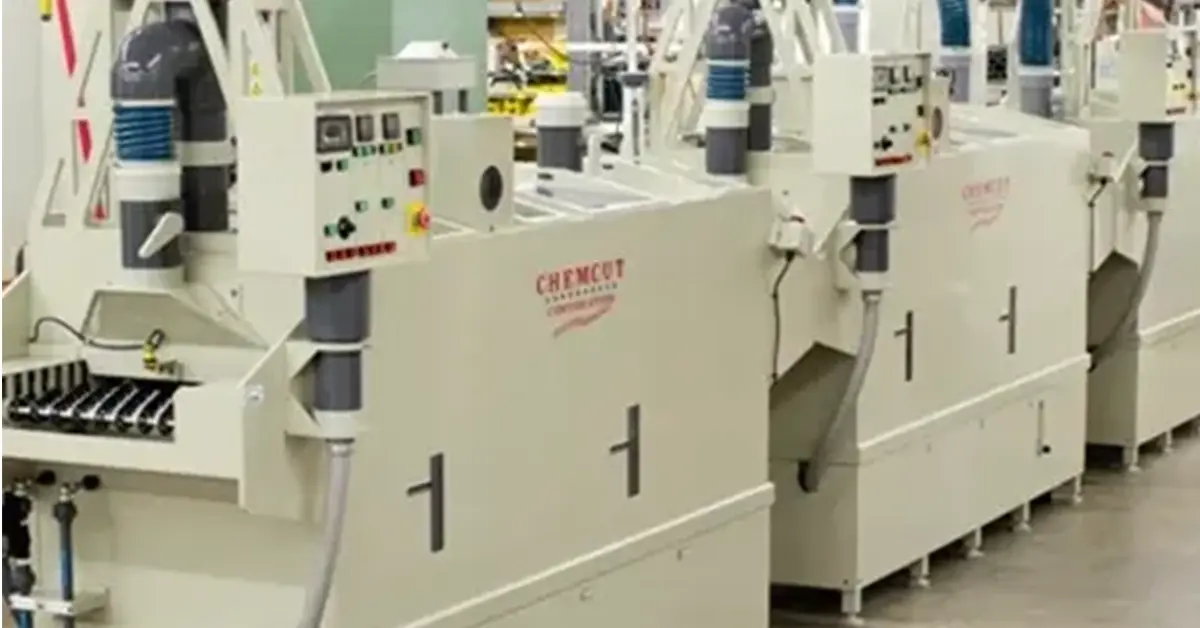
11 Things Needed to Start a Chemical Etching Plant | Chemcut Blog
11 Things You Need to Start a Chemical Etching Plant Chemical etching has been around since 2500...
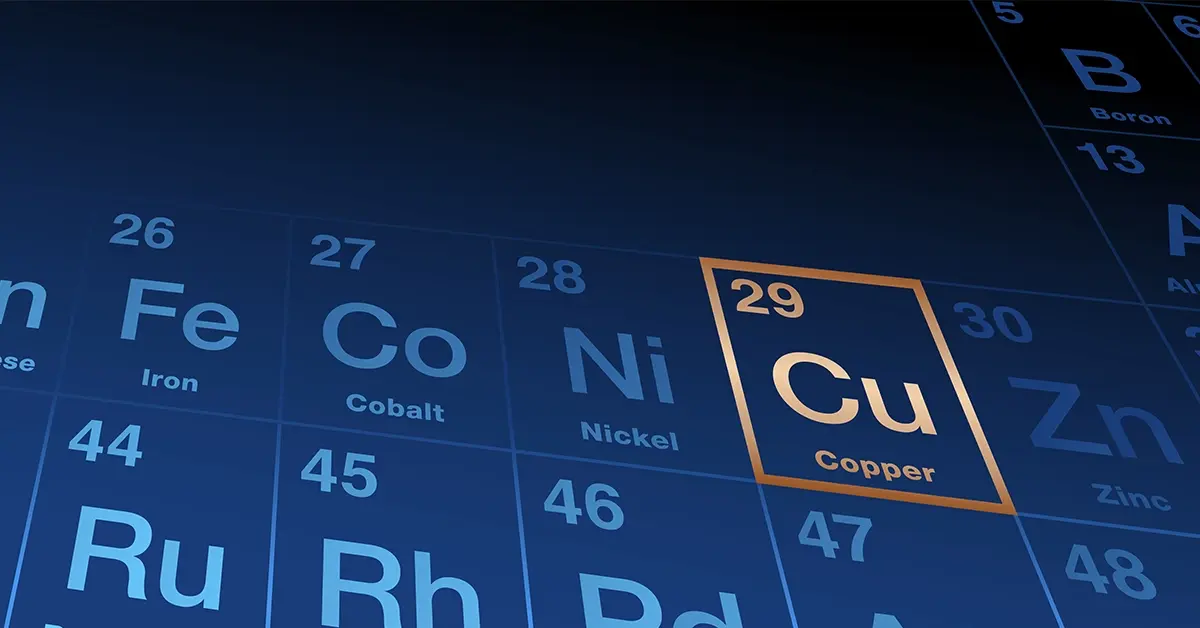
Copper Etchant Options | ChemCut
Copper etching is a vital manufacturing process that tends to be used in the manufacturing of...

Understanding The etching Process
Chemical etching is a widely used technique in the manufacturing industry for selectively removing...
High quality products are made with high quality equipment. Stake your reputation on Chemcut.
Already a customer?
Chemcut’s commitment to you goes beyond the sale. We keep your equipment running with the industry’s best post-sales support, which includes our in-house R&D lab and global field service assistance.
We also maintain the industry’s largest and most diverse inventory of high-quality replacement parts to ensure prompt delivery regardless of the type or age of your Chemcut or MEI Division equipment.