How and Why To Etch Titanium
Why Titanium Etching?
Titanium (Ti) is a versatile metal known for its heat resistance, corrosion resistance, high tensile strength to density ratio, and biocompatibility. These characteristics are the reason why Ti is highly used in the aerospace, medical, and automotive industries. There are many ways to work with Ti for manufacturing, but when it comes to working with sheet Ti or engraving Ti parts, chemical etching is the most efficient manufacturing method. Chemical etching titanium, compared to other methods such as laser cutting or stamping, creates a greater opportunity for large-scale production and an effective reduction in cost. If chemical etching of titanium is something that interests you, please continue reading to learn more.
Reactions/How to get different finishes?
Since titanium is a metal with high corrosion resistance, it is perhaps the most difficult metal to etch. This means it requires etching solutions with high electron affinity – thus only solutions that will etch titanium are Hydrofluoric acid (HF) and Ammonium Bifluoride (NH4HF2 – will refer to as ABF) Although these are both options for etching titanium, HF is the most practical etchant. HF is easier to handle than ABF (although both require extensive safety precautions), and it has an etch rate that is suitable for production. The etch reaction between titanium and HF can be seen below.
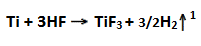
As you can see, by using HF we can effectively etch Ti. However, this reaction causes the production of hydrogen gas (H2) – which is not ideal. With the production of H2, more safety obstacles are introduced because it is highly explosive. To reduce the production of hydrogen during this reaction, nitric acid (HNO3) is introduced into the reaction (see below)

Notice that nitric acid prevents the evolution of hydrogen gas. Another benefit of using an HF and HNO3 mix for etching is that it will etch faster than the etchant with only HF (see Fig 1).1

Nitric acid can also be used to control the finish of the etch. If you have a particular roughness that you are looking for, you can vary the nitric acid to get the surface roughness you need (see Fig 2).

In some cases, if you need a specific roughness for your titanium, you may need a second treatment after you etch to obtain your desired features. One area of focus when it comes to technology with Ti is wettability. Wettability can be described as how hydrophilic a surface is. This area can be important to titanium because maximizing the contact area can maximize heat transfer in water, also wettability in terms of implants is important because the greater the wettability the easier it is for the implant to bond to tissue or bone. Methods of treating surfaces for wettability can include soaking in sodium hydroxide (NaOH) or potassium hydroxide (KOH).2
Chemcut has been building conveyorized HF etching equipment since the 1960’s. We have the most experience in the industry when it comes to titanium etching and handling of HF. If you have any questions about chemical etching of titanium, please send us your questions through our contact page or give us a call.
References
- Randy Markle. “Etching Titanium with HF and Nitric Solutions Part 1” Chemcut.net
- Kim, Christina et al. “Comparison of titanium soaked in 5 M NaOH or 5 M KOH solutions.” Materials science & engineering. C, Materials for biological applications vol. 33,1 (2013): 327-39.