Electroless Plating / Electrolytic Plating Equipment for PCB
Product Lines for Electrolytic and Electroless Plating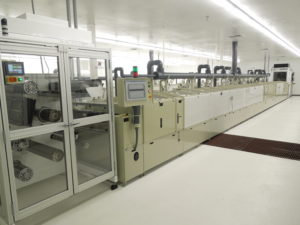
CC8000
Dip Tanks
XLi
2300 Series
What Industries use Chemcut Electroless and Electrolytic Platers?
Our electroless and electrolytic platers are designed for the PCB fabrication industry. Since our equipment is designed for flexibility and customization, it makes our machines a great solution for any plating or wet processing project.
The majority of our plating projects are conveyorized plating so they can be integrated into a conveyorized PCB fabrication process.
What Plating Systems do We Offer?
We can help you design and build your plating line in support of Printed Circuit Board manufacturing (PCB).
Horizontally conveyorized plating systems are available for desmear, activation, and electroless copper plating processes, including plated through holes (PTH). Other supported plating processes include electroless Nickel plating, immersion Tin process, immersion silver process, and immersion Gold.
Vertical plating lines are available for electroless plating of copper, electroless plating of nickel, electrolytic copper, electrolytic tin, electrolytic silver, and electrolytic gold.
Chemcut will build systems that incorporate electroless plating as needed (horizontal). For electroless processes, a supplier’s chemistry can be tested in one of Chemcut’s smaller spray tools, the 2300 series.
Construction in both CPVC and PP is available for use and testing in immersion chemistry can also be done in our research and development lab.
But for actual plate up and metallic resist plating, electrolytic is done on a vertical line with a hoist that can be programmed for semi-auto operation.
Desmear
Electroless Copper Plating
Electroless Nickel Plating
Electrolytic Copper Plating
Electrolytic Gold Plating
Electrolytic Silver Plating
Electrolytic Tin Plating
Immersion Gold Plating
Immersion Silver Plating
Immersion Tin Plating
Ni/Au Plating
PTH (Plated through-hole) Any discussion on this topic should include your chemistry supplier as well. It is critical that the bath for PTH is monitored closely.
Inner layer bonding operations: brown oxide (Bondfilm, Multibond, etc.), (white ‘oxide’ – immersion Tin)