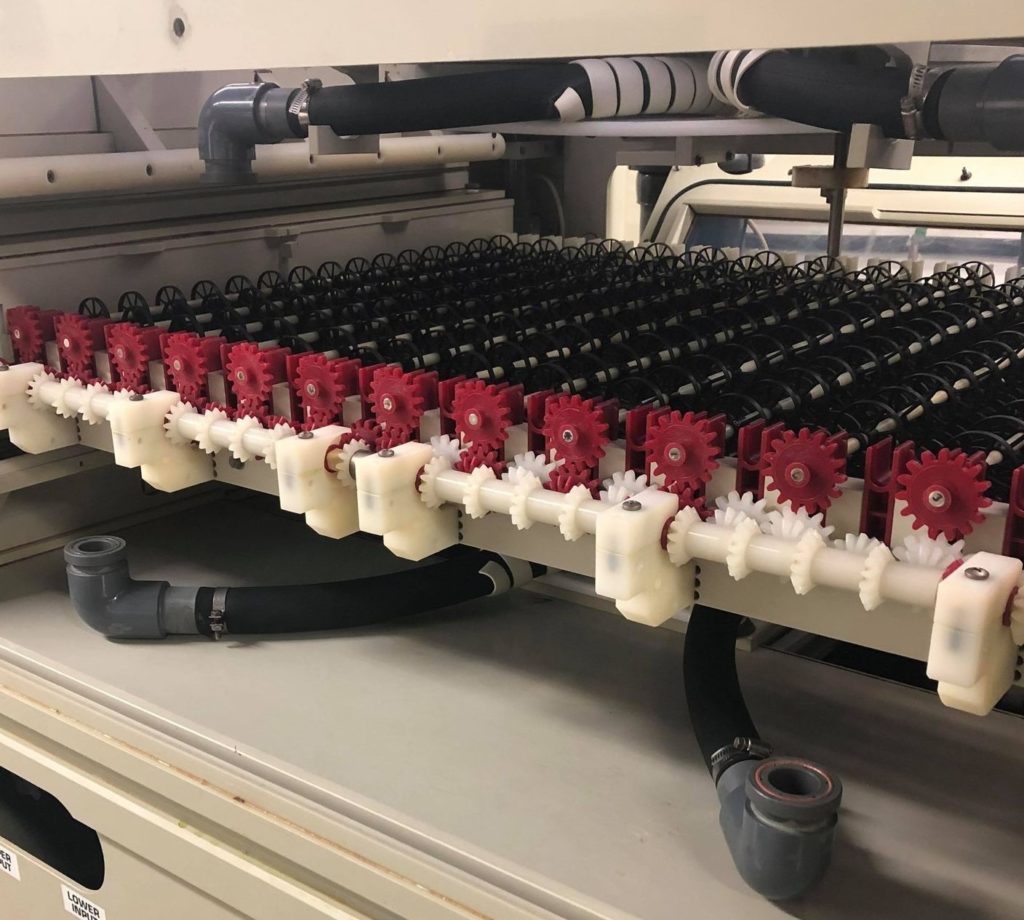
4 Reasons Your Chemical Etching Plant Needs Preventive Maintenance
In our last post about chemical etching, we explored the 11 things you would need to start a chemical etching plant. In that article, the focus was on what equipment was going to be necessary to etch metal for any commercial purpose. Although the article covers most of your needs, it does not cover everything. Another thing that is highly important to your chemical etching plant is a preventive maintenance program.
Preventive maintenance (PM) is one of the most important and most ignored matters in chemical etching. The main purpose of a preventive maintenance program is to keep the equipment in peak operating condition. If it moves or interacts with chemicals, it will wear with time. Having a preventive maintenance program not only benefits you by keeping your equipment operable; it also improves production scheduling. In this article, we will go over the 4 primary benefits of having a preventative maintenance program.
1. Machine Longevity
Having a successful chemical etching plant means more than just producing a lucrative product. It also means getting the most out of your equipment. Many Chemcut etchers have been in service for over 30 years, but that would have not been possible without preventive maintenance.
Over time, machine parts will receive wear and tear. Even in the cleanest environments, housings and drive shafts will corrode. Conveyor wheels and rollers will eventually swell, become brittle, or loosen on the conveyor rod because of the chemistry. Taking care of your equipment means taking care of the parts that go into it. By doing this you can make parts last longer so they do not need to be replaced as frequently.
2. Increased safety
Since working in the chemical etching industry means working with chemicals that are highly corrosive and toxic, containment of those chemicals is highly important. To prevent unexpected events of exposure, it is important to perform inspections often. Always check seals, plumbing, and containment to ensure there is no compromise. In addition to preventive maintenance, you should use other safeguards like adequate ventilation, containment trays, and other types of engineering controls. No one should only rely on PPE.
To maintain adequate containment, keep an eye out for excessive crystal formation. Crystal formation is primarily a problem that comes from leaks or failing gaskets. They can also get in the way of creating a seal and lead to more drastic leaks over time.
Chemically compatible materials are key to safety too. Since the chemicals tend to damage materials over time, it is a good idea to keep an eye on your tubing and seals. Often the rubber-like materials become areas of attack, and some people may not be aware of the compatibility while replacing them. If an incompatible part is mistakenly used, it is good to catch it early before it fails.
3. Equipment Efficiency
Cleaning your equipment is a great form of preventive maintenance that can go a long way. Your etcher will be more efficient if all the nozzles, spray tubes, and filters are clean. If you are starting to under etch or your etch is no longer uniform, this is an indication that your nozzles need cleaning. Knowing when to clean your nozzles is clear, but knowing when to clean your filters and spray tubes is more difficult. Spray tube blockage and clogged-up filters will increase the load on the pumps. Signs of this could be the pumps heating up more than usual or unusual sounds while running.
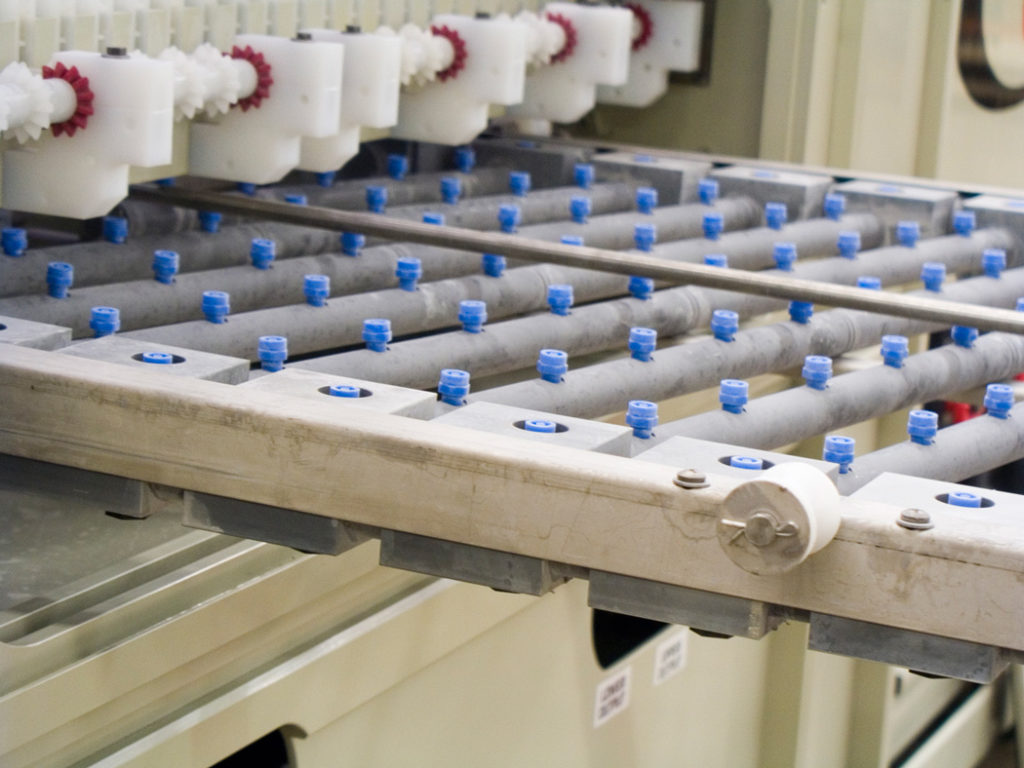
Cleaning is a major step because some metal etching processes can create by-products. If your etch line operates with a regeneration process to keep the etchant fresh, a by-product of the reactions could be a solid that will contaminate your bath. Often the contaminant from regeneration is salt, and if it is not cleared from the machine regularly, it will build-up and reduce your equipment’s efficiency.
When it comes to most processes in chemical etching, there are many variables that can directly affect the outcome of your product. Since these factors can lead to bottlenecks and high scrap rates, it is recommended to frequently check the heating and cooling performance, calibrate the probes, and clean the nozzles.
4. Reliability
Cleaning and replacing worn-out parts regularly will increase your wet processing equipment’s longevity and reliability. Lack of PM will result in emergency maintenance and unexpected downtime which could prove to be expensive. If a part were to break in the middle of a big project, your product may be late because of the time needed to diagnose the problem, receive the replacement part, perform the maintenance, and ensure the process is working again. This problem becomes magnified with more complicated pieces of equipment because of the unique parts and fine-tuning needed before continuing. By scheduling preventive maintenance around your big projects, you reduce the risk of downtime. If downtime does occur, it will not be as extreme as the case where maintenance was not been recently performed.
Having a preventive maintenance program will improve your chemical etching plant. With it, your equipment will be more long-lasting, safe, efficient, and reliable.
At Chemcut, we offer an extensive preventive maintenance agreement that is customer-specific. This program could be annual, semi-annual, monthly, or whichever works best for you. Chemcut would schedule a service technician to your facility to perform the preventive maintenance on the equipment, utilizing a PM check sheet as a guide. Should you be interested in this type of service, please contact our service department.